ER1100
Alloy 1100
Aws A5.10-17
Alloy 1100 is highly resistant to chemical attack and weathering. It is a relatively soft alloy that is very formable and is used extensively in thin gauge and foil products. It has good welding characteristics and it is also used as a filler alloy for welding purposes. A desirable characteristic of the alloy is the bright finishes obtained by anodizing.The products meet the requirements of AWS Specification A5.10, making them suitable for critical welding on heat exchangers, food manufacturing equipment, transportation equipment, and boating and shipyard applications. Aws a5.10: 1992 Superseded View Superseded By Superseded A superseded Standard is one, which is fully replaced by another Standard, which is a new edition of the same Standard.
ER2319
Alloy 2319
Alloy 2319 was developed as a filler alloy for alloy 2219 that is widely used in high strength structural and aircraft applications where superior resistance to stress corrosion cracking and high elevated temperature properties are desired. The alloy is heat treatable and provides higher strength and better ductility than the 4XXX filler alloys when welding 2XXX alloys.ER4043
Alloy 4043
Alloy 4043 is one of the oldest and most widely used welding and brazing alloys. Almigweld and Altigweld 4043 can be classed as a general purpose type filler alloy. The silicon additions result in improved fluidity (wet-ting action) to make the alloy a preferred choice by welders. The alloy is less sensitive to weld cracking and produces brighter, almost smut free welds.ER4047
Alloy 4047
Alloy 4047 was originally developed as a brazing alloy (BAlSi-4) or (718) to take advantage of its low melting point and narrow freezing range. In addition, it has a higher silicon content than 4043, which provides for in-creased fluidity and reduced shrinkage. The alloy produces bright and almost smut free welds. How cracking is significantly reduced when 4047 is used as a filler alloy. The alloy may be used in applications of sustained elevated temperatures.ER4145
Alloy 4145

Alloy 4145 was originally developed as a brazing alloy because of its low melting temperature and high fluidity. It provides very low susceptibility to weld cracking when used with 2XXX series alloys or, aluminum-copper, or aluminum-copper-silicon castings. It can be used in elevated temperature service applications. The alloy is often preferred over alloy 2319 when MIG welding because it 'wets' out better, provides a brighter looking weld, and produces less smut. It does, however, have lower weld tensile strengths than alloy 2319, and it is not suited for welding high magnesium containing alloys.
ER4643
Alloy 4643
Alloy 4643 is used for the welding of heavy sections of certain aluminum alloys when multiple weld passes are used and dilution of the base metal into the puddle is negligible. Post weld solution heat treat-ment and artificial aging may develop 90% of the tensile strength of the unwelded base metal in alloys 6061, 6063, 6070, and 6071. This alloy could also offer advantages in brazing type applications on thin sections where dilution ratios are low. Welds made with alloy 4043 or 4643 filler metal should have approximately equal performance in the as-welded condition. Alloy 4643 is very similar in weldability to 4043. The weld cracking characteristics, flow, pre-cleaning and machine settings are the same for this alloy as for 4043. The corrosion resistance is very good and equals or exceeds alloy 4043 in the weld zone and heat affected regions.ER5183
Alloy 5183
Alloy 5183 was originally developed in 1957 to provide the highest strengths possible in the as-welded condition of alloy 5083 and other similar high magnesium alloys. The more common filler alloy 5356, will typically fail to meet the as-welded tensile strength specification requirements of alloy 5083. The alloy is typically utilized in marine and structural applications where high strengths, high fracture toughness for impact resistance, and exposure to corrosive elements are important the alloy is not recommended for elevated temperature applications due to its susceptibility to stress corrosion cracking.ER5356
Alloy 5356
Alloy 5356 is the most widely used welding alloy and can be classified as a general purpose type filler alloy. Alloy 5356 is typically chosen because of its relatively high shear strength. The 5XXX alloy base material, welded with 5356, with a weld pool chemistry greater than 3% Mg and service temperatures in excess of 150°F are susceptible to stress corrosion cracking. Contact Alcotec for assistance in alloy and temper selection when elevated temperature service is a concern.ER5554
Alloy 5554
Alloy 5554 was developed as a filler alloy, primarily for alloy 5454 that is widely used in the manufacture of chemical storage tanks, automotive wheels, and in particular, those applications that may be subjected to temperatures in excess of 150°F. This combination of alloys does not become sensitive to stress corrosion cracking at elevated temperatures.ER5556
Alloy 5556
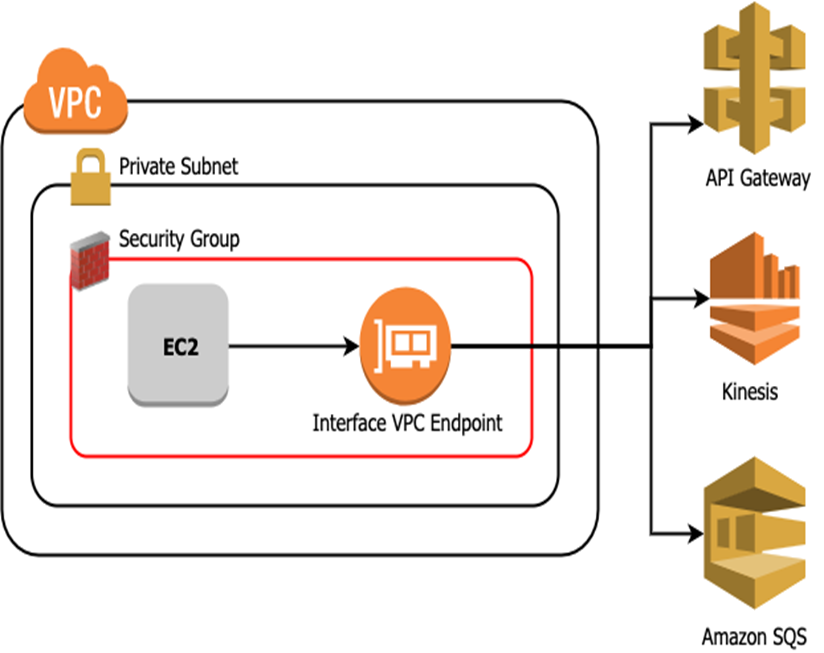
ER5654
Alloy 5654
Alloy 5654 was originally developed in 1968 to provide controlled low limits of manganese and copper. The result was a unique filler alloy that can be used to weld tanks for storage of hydrogen peroxide. This alloy contains more than 3% magnesium, therefore it is not recommended for elevated temperature applications due to its susceptibility to stress corrosion cracking. Exposure to certain corrosive chemicals requires special controls on the elements that make up the aluminum alloys that are used to contain them.
206.0
Alloy 206.0
Alloy 206.0 is alloyed with copper to provide high tensile properties in the heat treated condition. Disadvantages include limited fluidity and poor resistance to hot cracking. The alloy is also susceptible to stress corrosion cracking in a fully hardened (heat treated) condition.This filler wire is designed for joining or repairing aluminum copper alloy castings. In this application, the weld zone will respond to heat treatment with properties, and corrosion resistance comparable to those of the casting. AlcoTec produces alloy 206.0 in both spooled and straight length form.R-C355.0
Alloy 4009
R-C355.0 (Al-Si-Cu-Mg) is alloyed with copper to afford a greater response to heat treatment (higher strength) but inversely sacrifices ductility and corrosion resistance. Alloy R-C355.0 contains a low amount of iron to create higher tensile properties in premium quality castings. This filler wire is designed for joining and repairing 355.0, A355.0, and R-C355.0 castings and is available in both spooled and straight length form. Alloy R-C355.0 when fabricated as a wrought wire product, is registered by the Aluminum Association as Alloy 4009.
A356.0
Alloy A356.0
Alloy 4008 is used in large quantities for sand and permanent mold castings. Alloy 4008 is a tightly controlled chemistry version of A356.0 (4010). We recommend a maximum brazing temperature of 1035°F.357.0
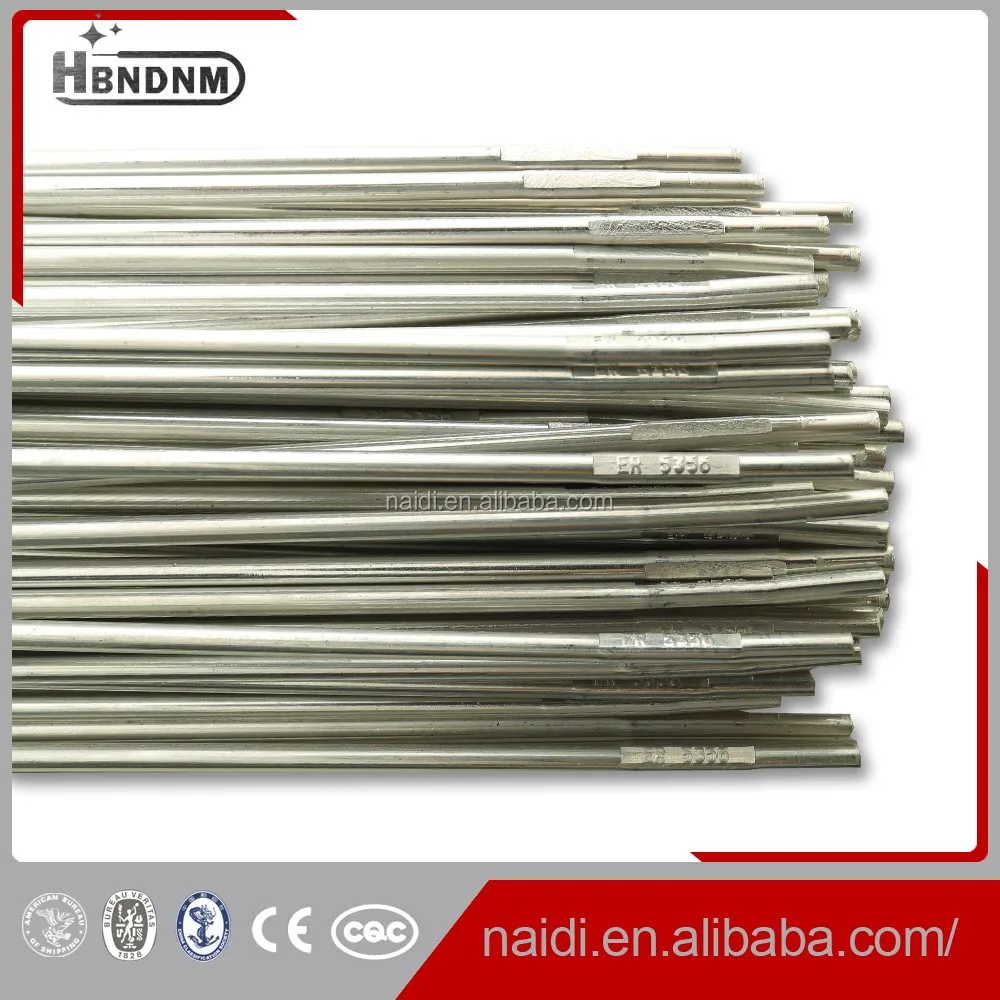
Aws A5.10
Alloy 357.0
Alloy 357.0Aws A5.10 Er5356
was designed to produce a tensile strength greater than that normally found using Alloy A356.0. The higher properties, when compared in the -T6 temper, are a result of the chemistry differences. Specifically Alloy 357.0 has an average magnesium content of 0.5%. These premium castings are typically marketed for aerospace applications. Alcotec controls the 357.0 chemistry to also meet the tighter limits of 357.1 base metal. We recommend a maximum brazing temperature of 1030°F.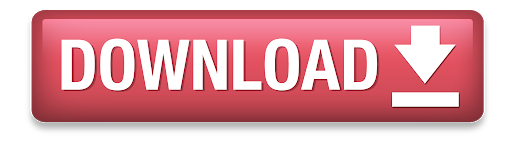